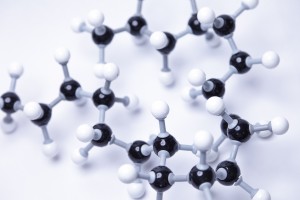
We’ve already established heat is the Achilles heel of many types of plastic, and we’ve discussed how heat additives can help improve a polymer’s resistance to damage from extreme temperatures. Additionally, we can use heat to our advantage in the world of polymer testing. To understand how thermal testing is useful, it helps to first know why plastic melts in the first place.
Why does an otherwise amazingly durable and versatile material have trouble withstanding heat? It has to do with the nature of heat — energy related to the movement of molecules — and how polymers are formed.
Polymers are large chains of molecules, and heat is what you get when the molecules in a material respond to radiation and start moving. The radiation may be sunlight (think melted video cassette on a car seat), microwave (remember our exploding egg experiment?) or another type that causes the molecules to move and release energy. That energy can make molecules move out of alignment which, in a polymer, can alter how the material behaves in the real world. It can also cause those molecules to separate into components we can quantify through thermal testing.
By analyzing the temperature transitions, chemical reactions and viscoelastic properties of samples when heated, we can learn about how it was processed, what components of the polymer are or whether it is made up of multiple components, and how it might behave when exposed to heat in manufacturing processes or in real-world applications.
In addition to compositional information about a polymer, thermal testing can also provide a very important — and basic — bit of information: the temperature at which the polymer will soften or melt. This is critical information in many polymer applications.
For example, heat-resistant polymers used in construction and manufacturing can help slow or even halt the spread of fire in structures where firefighting can be problematic, such as skyscrapers, airplanes and boats. If a manufacturer finds the supposedly heat-resistant polymer-coated wiring they intended to use in construction isn’t as heat-resistant as they thought, they need to take steps to improve the polymer, such as adding heat stabilizers into the formulation.
Depending on how you look at it — and what you intend to use your polymer for — heat can be used for the good and the bad. It takes scientific knowledge to turn a material’s heat resistance (or lack thereof) to the manufacturer’s advantage!