Product and materials testing isn’t a one-and-done activity. Even though a product or material has been fully developed and undergone a barrage of tests to demonstrate it will do what it’s intended to do, that doesn’t mean testing can end. Unexpected events could occur and a product that performs in one way today could behave in a different and unexpected way tomorrow depending on several factors. That’s why routine testing of polymer materials and products is important.
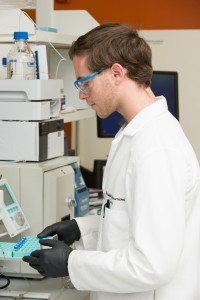
“Routine testing” is far less hum drum than the name might imply. This ongoing testing helps companies monitor the performance of their products, materials, and formulations, address concerns that emerge as the product functions in the real world, and understand changes needed to improve the product down the road. In fact, routine testing of medical device polymers is critical to ensure the product meets specifications, behaves as intended and is safe for patients.
This is especially important for bioabsorbable medical devices made from bioabsorbable polymers. Because these devices are designed to be absorbed into a patient’s body over a designated time frame, critical properties, such as molecular weight, need to be within a specified range. A device that dissolves too quickly may be absorbed before a patient completely heals, and one that dissolves too slowly could cause infection and other complications. In addition to molecular weight, routine testing can encompass a number of other considerations such as; irritation, sensitization, genetic toxicity, and toxicology.
Polymer Solutions does a lot of routine testing for our clients, some of which include medical device manufacturers. The testing typically evolves in tandem with the product and process development phases with the ultimate goal to create a routine test that will provide relevant, timely and validated analytical protocols. We use instrumentation and testing, some of which include; Residual Monomer Testing, Fourier Transform Infrared Spectroscopy, Nuclear Magnetic Resonance Spectroscopy. Besides medical devices, we routinely test polymer-coated fabrics, cure-in-place pipes, and composite panels.
While routine testing establishes an ongoing stream of data about how a product or material performs in real-life applications, each routine testing process presents an unique set of challenges and objectives. We may do it every day, but we know there’s nothing mundane or boring about routine testing when you consider its vital role in ensuring patient safety.