One of our medical device clients contacted us because one of their products, an anodized aluminum surgical drill, was experiencing defects in the coating. Testing was requested to examine the aluminum composition, the coating composition, and the coating thickness to determine the reason why the anodized coating could be coming off at an accelerated rate.
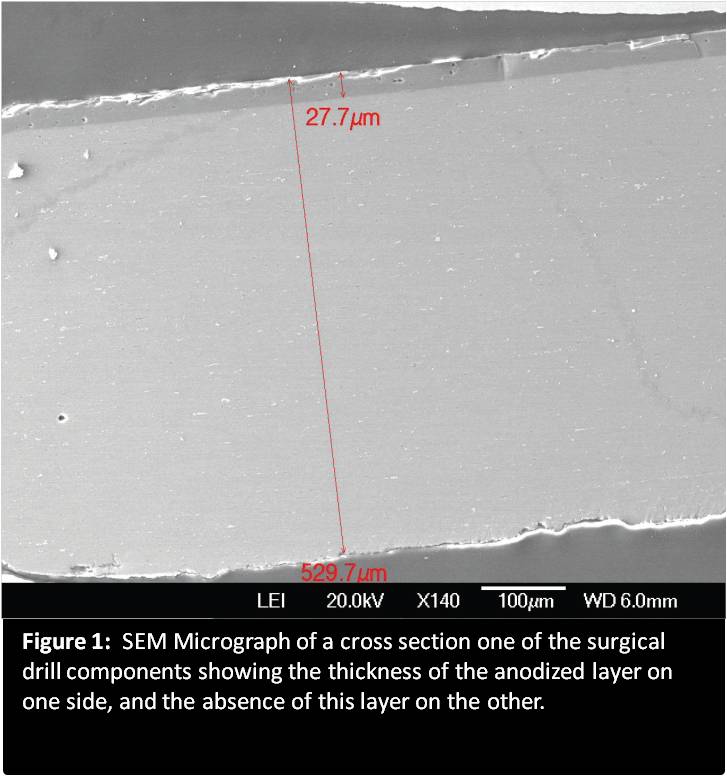
The surgical drill had components of anodized aluminum, polysulfone, and stainless steel. Our initial approach was to use optical microscopy to examine all the components of the device, not just the aluminum parts. The polysulfone components of the drill, as well as the stainless steel parts, did not have any surface damage, although they were adjacent to and touching the anodized aluminum. Multiple samples were demonstrating the defect with some showing more severe pitting than others. Pitting is a form of localized corrosion in which there are very small holes within the coating. Examination also revealed that all the anodized aluminum parts were experiencing corrosion from pitting.
The next technique we used for this corrosion analysis was Scanning Electron Microscopy with Energy Dispersive Spectroscopy (SEM-EDS). SEM-EDS was used to examine the sample’s bulk alloy composition, the anodized coating composition, the anodized coating thickness, and to identify if any corrosion products were on the surface.
Examination of an aluminum sample area, which had an anodized coating, revealed that the coating was missing from the exterior face portion of the device. Further examination of the sample in an area that had been protected by a rubber component revealed that there was still a uniform anodized coating.
EDS confirmed that the alloy of the samples was consistent with Aluminum 6061. This ruled out the possibility that an alloy was used that was not compatible with the anodizing process. EDS of the samples also confirmed that anodization process had initially been successful since the locations that had an intact coating showed the presence of aluminum oxide with some sulfur, consistent with anodization.
Examination of the anodized coatings on the damaged samples indicates uniform pitting is the likely corrosion mechanism. The four mechanisms which could remove an anodized coating include: heavy metal exposure, galvanic corrosion, chlorine exposure, or extreme pH environments (outside 4-9 pH).
It was reported by the client that the washing procedure for the medical device included deionized water, so we knew it was unlikely that heavy metals exposure was the culprit. Galvanic corrosion was also unlikely as it would exhibit as a more localized corrosion rather than corrosion all over the exposed surface, and the medical device was composed of mostly aluminum with limited amounts of higher potential metals such as stainless steel. While chlorine and low pH environments could remove the anodized coating, the excellent condition of the stainless steel and polysulfone parts indicated that this was likely not the cause of the corrosion. Chlorine can cause pitting to stainless steel and surface deterioration to polysulfone, and low pH environments are just as harsh to stainless steel as to anodized aluminum.
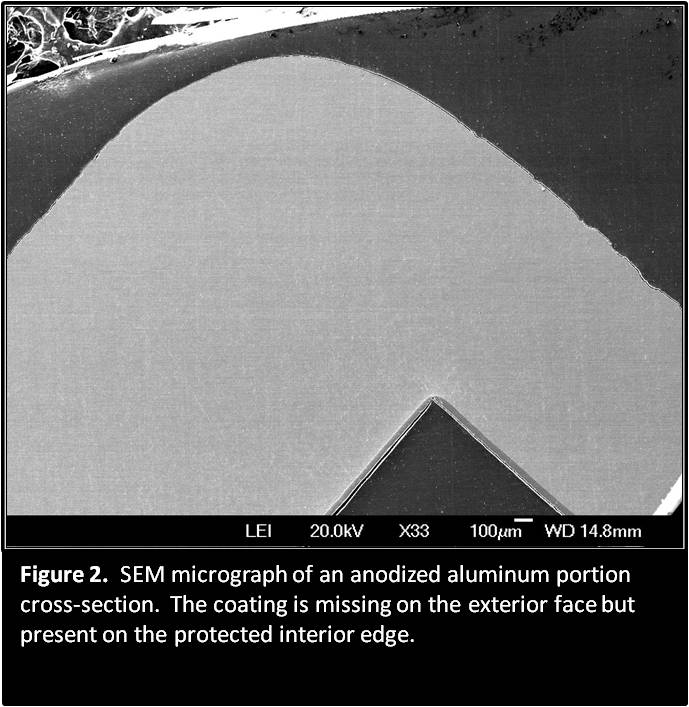
Based on the totality of our coating defect investigation, we determined a high pH environment (pH 9+) is the most likely cause of the pitting corrosion observed on the anodized aluminum part. Chemicals such as sodium hydroxide and sodium carbonate can easily raise the pH of aqueous solutions to be capable of stripping the anodized coating from aluminums, and those solutions would not harm steels unless the pH was higher than 12. Unfortunately, corrosion of the anodized coating caused by caustic solutions would not leave an identifiable corrosion product behind as the Al2O3 converts into an aluminate anion. It is recommended that future testing involve analyzing the cleaning solutions used on the drills to determine their chemical composition and pH to confirm whether they are capable of removing the anodized coating.
After examining the anodized coating with optical microscopy, measuring the anodized coating thickness, confirming the coating composition, and analyzing the composition of the bulk aluminum alloys, the most likely cause for the accelerated anodized coating removal is from repeated exposure to a high pH (9+) environment during the cleaning cycle.