In the world of polymer science, a single, seemingly small change in a polymer’s molecular structure can have a huge impact on how a material behaves in the real world — and on the products you make from that material. Polymer “kissing cousins” PVC and CPVC illustrate this concept brilliantly.
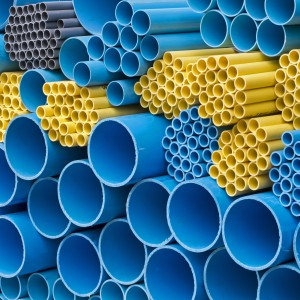
PVC (polyvinyl chloride) has been around since the late 19th century, but didn’t have widespread use until after World War II. Today, its strength, durability, relatively low cost, and easy utility make it a top choice for plumbing and drainage applications. If you’ve ever passed a construction site — commercial or residential — you almost certainly have seen multiple choices of PVC pipes being used for plumbing or ductwork. However, as great as it is, PVC can only handle fluids up to around 140°F.
Enter PVC’s cousin, chlorinated polyvinyl chloride (CPVC). Both PVC and CPVC are essentially the same molecule, with one simple, yet significant difference — during the manufacturing process, the use of a free radical chlorination reaction boosts the chlorine content of CPVC. The chlorine content is increased from 57% to as high as 74%. That simple alteration affects how CPVC behaves in real-world applications.
The most significant difference is CPVC’s improved heat resistance. It can handle fluids up to about 200°F — making it a better choice than PVC, for hot-water plumbing. If you pipe water that is too hot through PVC pipes, they could melt, crack and leak — leaving you with a literal hot mess!
However, CPVC has a big vulnerability, one that it shares with PVC — it is susceptible to environmental stress cracking (ESC) by phthalates, such as diisononyl phthalate (DINP). DINP is a plasticizer commonly used to make PVC more flexible, and its use allows us to have vinyl car seats (Oh yay!), super-thin electrical cable insulation, and rust-resistant car bumpers. It’s also commonly used in sealants — and therein can lie a problem.
Recently, a client asked us to help them understand why a CPVC pipe had failed. We suspected a caulk containing DINP had been in contact with the pipe.
We conducted an environmental stress cracking experiment. We inserted a large metal ball bearing inside a piece of pipe to create significant hoop stress, applied a drop of DINP to the exterior of the pipe (over the location of the ball), and then videotaped the pipe for 15 hours.
The experiment perfectly illustrated a vulnerability that PVC and CPVC have in common. You can see the test results here — where we compressed the 15 hours to a 90-second video. This visual is eye opening!