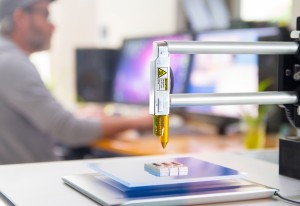
From an artificial skull made of acrylic to custom confections created from chocolate, the world of 3D printing keeps getting more amazing. Today, 3D printers can allow people to create virtually anything, using a variety of materials, from metal and ceramic to sugar and Styrofoam. Of course, plastic is the substance that first made 3D printing of any kind possible, and plastic remains one of the most common and versatile types of materials used in 3D printing.
A commenter on a recent Polymer Solutions blog asked for information about the most common types of plastics used in 3D printing. Here’s a little bit about the three most-frequently used plastics that have helped spur the amazing evolution of 3D printing:
Polylactic Acid (PLA) — It’s probably no surprise that one of the most commonly used bioplastics in the world would also dominate in 3D printing. A biodegradable thermoplastic aliphatic polyester, PLA is made from renewable, organic resources like corn starch or sugarcane. It’s commonly used to make food packaging and biodegradable medical devices and implants. PLA is great for 3D printing because it’s easy to work with, environmentally friendly, available in a variety of colors, and can be used as either a resin or filament.
Acrylonitrile butadiene styrene (ABS) — A terpolymer fabricated by polymerizing styrene and acrylonitrile with polybutadiene, ABS is another plastic commonly used in 3D printing. Beginners especially favor it for its ease of use in its filament form, and because it’s durable, strong, heat-resistant, cost-effective and flexible. However, because it’s petroleum-based and not biodegradable, ABS is losing popularity among 3D hobbyists who prefer the more eco-friendly nature of PLA. Also, when heated in a 3D printer for the fabrication process, ABS can give off fumes that might be irritating.
Polyvinyl Alcohol Plastic (PVA) — A water-soluble plastic, PVA is most commonly used as a glue, thickener or packaging film. In the world of 3D printing, PVA isn’t necessarily used to make the finished product, but rather to create a support structure for portions of a product that may warp or collapse during the printing process. In printers with two or more extruders, the user can employ one or more extruders to create a support structure of PVA while the others work to create the actual product out of other materials. When the printing is done, the finished and cured product can be dunked in water until the PVA support structure dissolves away.
Of course, the range of materials that can be used in 3D printing continues to expand and evolve along with the process and its applications. Still, one of the most amazing developments in manufacturing traces its beginnings to the original “space-age” material — plastic. And that strikes us as very fitting!